Innovative Wooden Bead Making Technology from IIT Delhi’s RuTAG Transferred to Harraj Industries for Production
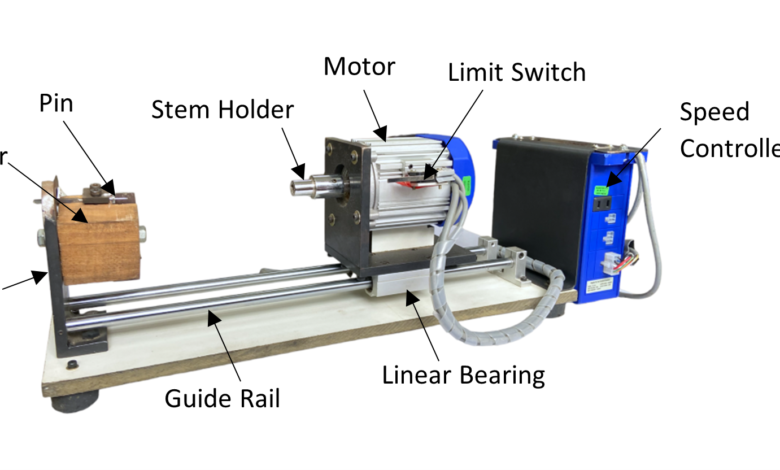
The Rural Technology Action Group (RuTAG) at the Indian Institute of Technology Delhi (IIT Delhi) has successfully transferred the fabrication technology of an AC motor-powered wooden bead-making device to Harraj Industries. This technology aims to revolutionize the traditional bead-making process and bring substantial benefits to the rural sector, especially women artisans in Mathura, Vrindavan, and neighboring areas of Uttar Pradesh, India.
The technology, now under license with Harraj Industries, is set to be manufactured and commercialized. The design of the AC Motor-Powered Wooden Bead Making Device is safeguarded through design registration at the Indian Patent Office, and the transfer was facilitated by FITT-IIT Delhi.
Prof. SK Saha, Project Principal Investigator and IIT Delhi professor, shared, “The AC Motor-Powered Wooden Bead Making Device has undergone a decade-long evolution as a science and technology project. The dedicated efforts of the RuTAG IIT Delhi team have focused on improving ergonomics and reducing the drudgery faced by women artisans.”
The latest iteration of the device, conceptualized by IIT Delhi PhD student Mr. Yashwant Prasad, boasts nearly noiseless operation. This advancement has not only improved the working conditions for artisans but has also significantly increased daily production and earnings, from Rs. 700–800 to about Rs. 3000 per day.
Harpreet Singh, Proprietor of Harraj Industries, expressed plans to distribute the device through various channels, including the Government E-Marketplace (GEM) and other e-commerce platforms. This strategic approach aims to make the innovative wooden bead-making device easily accessible to exporters and other interested customers across the country.
The versatile device can craft spherical beads ranging from 5 mm to 25 mm in diameter from wood. It simultaneously performs turning and drilling operations, with an operational speed ranging between 2000 and 3000 rpm, facilitated by advanced speed control (variable frequency drive). The beads are predominantly crafted from Tulsi (Holy Basil) stems, primarily used to create garlands for devotees. This technology transfer marks a significant step toward empowering rural artisans and promoting sustainable practices in traditional crafts.